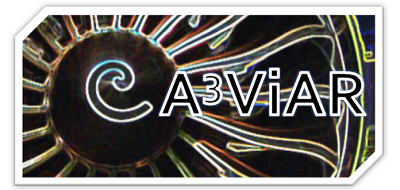
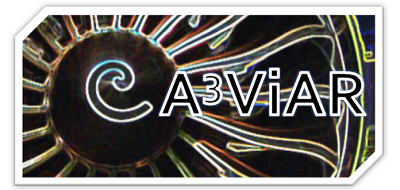
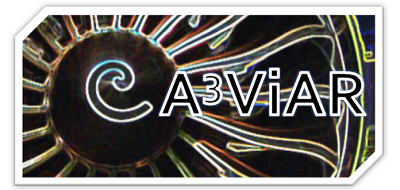
Driven by both economic and ecological requirements, airplane operators and thus manufacturers invest continuously in reducing the fuel consumption. Regarding the engines, a way to further reduce the fuel consumption is increasing the propulsive efficiency, which directly depends on the difference between the engine exit velocity and flight velocity. This has led to the development of UHBR engines equipped with larger fans, having a reduced pressure ratio and reduced speed.
The aim of the Composite fan Aerodynamic, Aeroelastic and Aeroacoustic VAlidation Rig (CA3ViAR) project is the design of a Low-Speed Fan (LSF) that will develop instabilities, which are representative for fans in ultra-high-bypass-ratio (UHBR) engines of civil aircraft. During the project, extensive experimental tests to measure aerodynamic, aeroelastic and aeroacoustic performance under a wide range of operational conditions will be performed. The resulting models, data and documents will be published as an open test case, which is unique in the engine fan research.
These Low-Speed Fans bring new challenges from aerodynamic and structural perspectives. The higher bypass ratio (BPR) increases the required operating range of the fan by moving Take-Off and Approach closer to the part-power limit of the fan and, therefore, reducing its stall margin and increasing the flutter risk. In parallel, the increased fan diameter is driving the intake design, with significant implications for drag and airflow inlet distortion at the Aerodynamic Interface Plan (AIP) under off-design and cross-wind conditions. By reducing the fan speed, the blade surfaces are aerodynamicly highly loaded, whereas the increasing diameter of the fan and the weight reduction of the fan blade itself leads to slender blade structures.
Therefore, the application of lighter and stiffer materials, such as carbon fibre reinforced polymers (CFRP) instead of more conventional titanium alloys, is essential. These materials will provide more degrees of freedom during the design process of the fan in terms of “customised” stiffness and inertia distributions along the blade span. This demands the development of more reliable and accurate methods for the aerodynamic, aeroacoustic and aeroelastic design of engine fans.
The CA3ViAR project, coordinated by IBK, is pursuing several objectives. As a first step a literature review of the main issues affecting composite UHBR engine fans is being performed by the Technische Universität Braunschweig (TUBS). The design of the Low-Speed Fan is being led by TUBS with support from DREAM, in terms of aerodynamic shaping, and from Leibniz Universität Hannover (LUH) and IBK, in terms of aeroelasticity and aeroacoustics. Adamant Composites (ADC) is responsible for the tasks related to the manufacturing of the composite blades and further new rig parts, e.g. the new designed stator vanes.
The LSF test rig, to be mechanically designed by IBK, is being conceived to experience aerodynamic and aeroelastic instabilities during wind tunnel operations. The supervision of the manufacturing is the responsibility of IBK, including the placement of subcontracts with well-recognized manufacturers specialised in rotor blades and parts made of both composites and metals, while requirements for the test rig integration are provided by TUBS, which is responsible for wind tunnel instrumentation and operations. The execution of the experimental tests measuring fan instabilities (e.g., stall, flutter, etc.) is performed by TUBS with support from LUH.
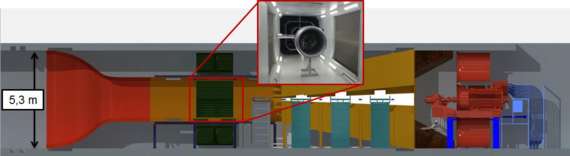
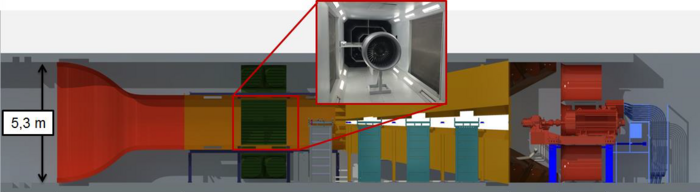
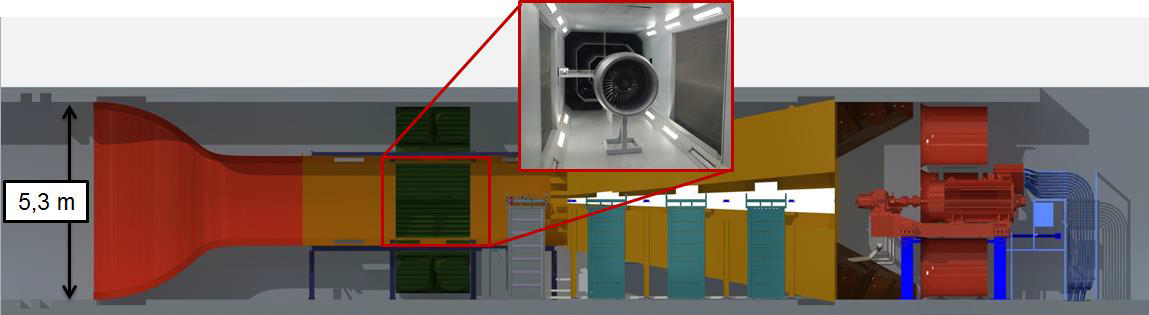
Experimental tests will be performed in the Propulsion-Test Facility (PTF) of the Institute of Jet propulsion and Turbomachinery (IFAS) in Braunschweig, Germany. The test facility is able to drive the LSF at a wide range of operating points, including operation points in critical off-design conditions. Take-off and side-wind conditions can be generated with the cross-wind tunnel section.
The last technical phase of the project is the calibration and the validation of aerodynamic, aeroelastic and aeroacoustic models using the wind tunnel test data acquired in the PTF. To obtain the test data with a high accuracy, advanced measurement techniques will be used in addtion to the standard techniques. Beside to the standard steady and unsteady aerodynamic measurement sensors situated on the surface, such as pressure taps and Kulites, particle image velocimetry (PIV) will be used to investigate the flow field of the LSF. The resulting vibrations due to the aeroelastic instabilities will be measured by a high-speed digital image correlation (DIC) setup, supported by tip timing, strain gauges, and accelerometers. The acoustic field in the intake of the LSF will be investigated with fast pressure-senstive paint (iPSP) and Kulites. This last technical phase is being led by LUH, with strong support from all other partners.
The project started in September 2019, and has a duration of 48 months.